The Vizag Gas Leak, categorised as an industrial accident which occurred at the LG Polymers chemical plant in R. R. Venkatapuram village on the outskirts of Visakhapatnam, Andhra Pradesh. In the wee hours of 7 May 2020, the styrene gas cloud spread over a radius of around 3 KMs which resulted in the death of 13 and more than 1,000 people got sick after being exposed to the gas. Styrene gas was leaked from a storage tank of LG Chem Polymers. The factory was first inaugurated in 1961, originally as Hindustan Polymers, to manufacture polystyrene which was then merged with McDowell & Co of the UB Group in 1978, then finally taken over in 1997 by LG Chem, which renamed it LG Polymers. The factory manufactures general-purpose polystyrene and high-impact polystyrene, expandable polystyrene, and engineering plastics compounds.
The main cause of this accident is categorised as a human error and negligence. Just after the incident a team of Andhra Pradesh Forensic Science’s officers was formed under Dr RK Sarin and T Suresh who visited the gas tragedy site and collected evidence.
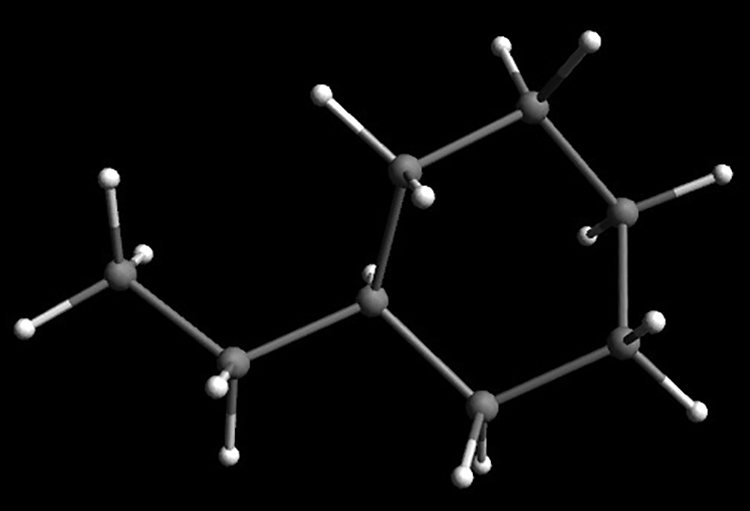
What is Styrene Gas?
Styrene, a derivative of Benzene (C6H6), is an organic compound with formula C8H8. It is stored as a liquid below temperatures of 20 degree centigrade. Styrene is the raw material for polystyrene, which in turn is used to manufacture plastic and rubber parts of such as computers, refrigerators, ovens, fibreglass etc. It is also used to produce co polymers which are derived from one or more species of monomers.
Although, Styrene is also some fruits and vegetables in small amounts, but breathing air containing styrene is the main route to get exposed to this chemical. Exposure to styrene affects the Central Nervous System and can cause breathlessness, respiratory problems, irritation in eyes, Gastrointestinal effects, nausea, transient loss of consciousness, etc. Several people reported acute breathlessness, a few of whom suffocated to death. People were seen coming out of their homes and collapsing on road catching their throat and rubbing their eyes. The panic-stricken people in turn ended inhaling more gas than they would have.
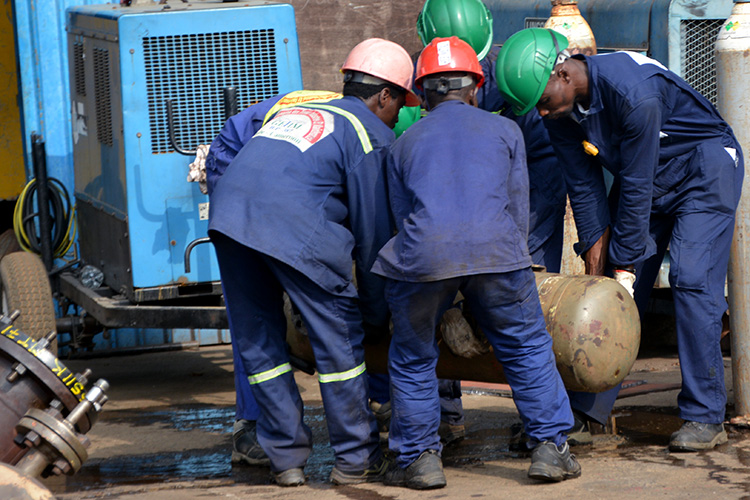
What caused the Accident?
Main cause of the accident is said to be human error and lack of proper maintenance during lockdown. The plant was scheduled to reopen on 7th May when the disaster took place. It is said that at the time of leak 14 workers were on duty who failed ring the alarm and escaped falling victim to the gas leak.
According to experts, styrene should be mixed with tertiary butyl catechol (TBC) to prevent self-polymerisation. But there is no evidence that it was ever added and whatever was left got exhausted, soon the self-polymerization started which led to a chemical reaction which generated enormous heat of 150 degrees centigrade. The cooling process was also not maintained and when this enormous heat was generated vapours started coming out of the breather. Styrene’s boiling point is between 135-145 degrees centigrade and should be maintained at 20 degrees centigrade, but temperatures upto 100 degree centigrade is considered as safe zone. When temperatures soar above 100 degrees centigrade, it would raise an alarm.
Even when the Andhra Pradesh Forensic Science Laboratory officers visited the disaster site, temperature of Styrene storage tank was hovering between 120-150 degrees centigrade. And, it took them almost 2 days to bring down the temperature to 80 degrees centigrade. There should have been an operator sitting in control room to verify and report and discrepancy.
The experts who visited the storage facility also noted that not all required safety and technical parameters were maintained. Also, polymerisation had just begun in another storage facility on the premises. The storage facilities were not designed to keep the material for a long period of time.
It is also worthy to note that the main issue of this accident is said to be lack of maintenance, but the district administration had issued 45 passes for the maintenance staff to work in three shifts. It would be determined by the investigators that when they were allowed the maintenance activities, then how such a lapse had occurred.
Although, the company has admitted the leak of vapour from styrene monomer storage tank near the general purpose poly styrene, still, the FIR registered by the police against the company has no mention of this gas. The FIR mentions the cause of disaster as some smoke and a bad smell that endangered life.
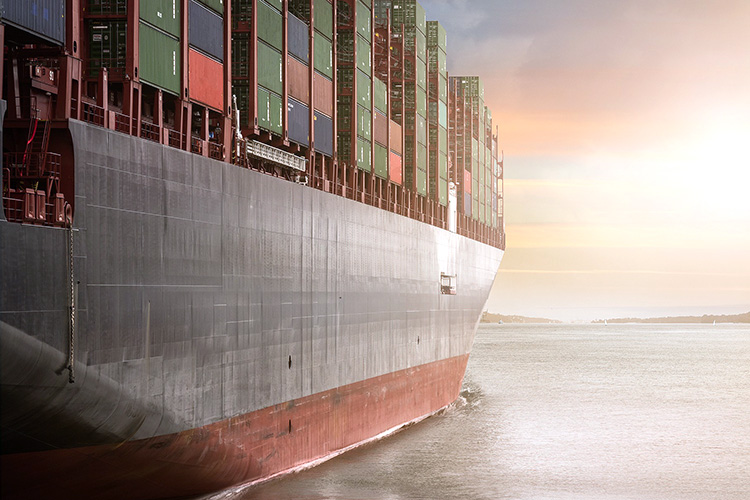
Legal obligations for the company
Soon after the incident an FIR was registered under Sections 278 (Making atmosphere noxious to health), 284 (Negligent conduct with respect to poisonous substance), 285 (any act with combustible matter to endanger life), 337 (Causing hurt by act endangering life or personal safety of others), 338 (Causing grievous hurt by act endangering life or personal safety of others), 304-II (Knowledge that the act had likelihood of causing death) of IPC.
An NGT bench headed by Justice Adarsh Kumar Goel ordered LG Polymers India to deposit an amount of Rs 50 crore as an initial amount with the Vishakapatanam DM to mitigate the damages caused due to the incident. A five-member fact-finding committee is also formed to probe the incident and deliver a report to the bench. B. Seshasayana Reddy, former Andhra Pradesh High Court Judge would be supervising the committee.
State Government had summoned the management of the plant from South Korea along with its team of experts who would work closely with the inquiry into the mishap. Soon after LG Chem has sent an eight member delegation led by its Business Head to India to investigate the cause of this accident that killed 11 people and sent 1,000 to hospital for treatment.
The Andhra Pradesh government had directed the company to immediately take 13,000 MT of material out of the country. For which the state government had arranged two vessels to carry 8000 MT and 5000 MT material out of the country back to their headquarters in South Korea.
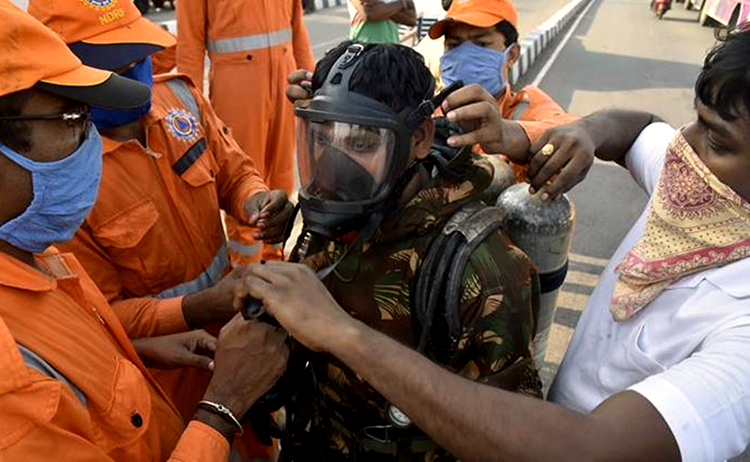
Cleaning the toxicity
The Industries and Commerce department of the Andhra Pradesh government had requested for 8.3 T of essential chemicals to effectively control the gas leak. The 8.3 tonnes of chemicals were airlifted from Gujarat by the India Air Force aboard two An-32 transport aircraft which airlifted approximately 1.1 tonnes of Tertiary Butylcatechol and 7.2 tonnes of Polymerization Inhibitors and Green Retarders from Mundra, Gujarat.
The civic body has carried out sanitisation drive covering public and private premises. Government has also sanitised the surrounding water bodies which were considered to be contaminated. Greater Visakhapatnam Municipal Corporation had stopped the supply immediately from Meghadrigedda as a precautionary measure. The water will not be drawn from Meghadrigedda till tests are conducted and it is proved that the water is safe for drinking. Villagers, who were returning home have been advised not to use groceries, which were left out in the open.
An expert panel, said that the May 7 styrene gas leakage has also contaminated the soil in the area. Agriculture products, including vegetables, cultivated here are not safe to consume at least for a year. Now it is being speculated that the chemical toxins could have polluted the groundwater too. Water was being sprayed in the villages to reduce gas density in the air. The Agriculture Minister K. Kannababu in his statement had said the state government has constituted a committee of medical and health experts to study the impact of the gas leak on the health of the public. The factory is now closed till further orders by the government.